Scope Creep Costing You Big Bucks? Here's What to Do
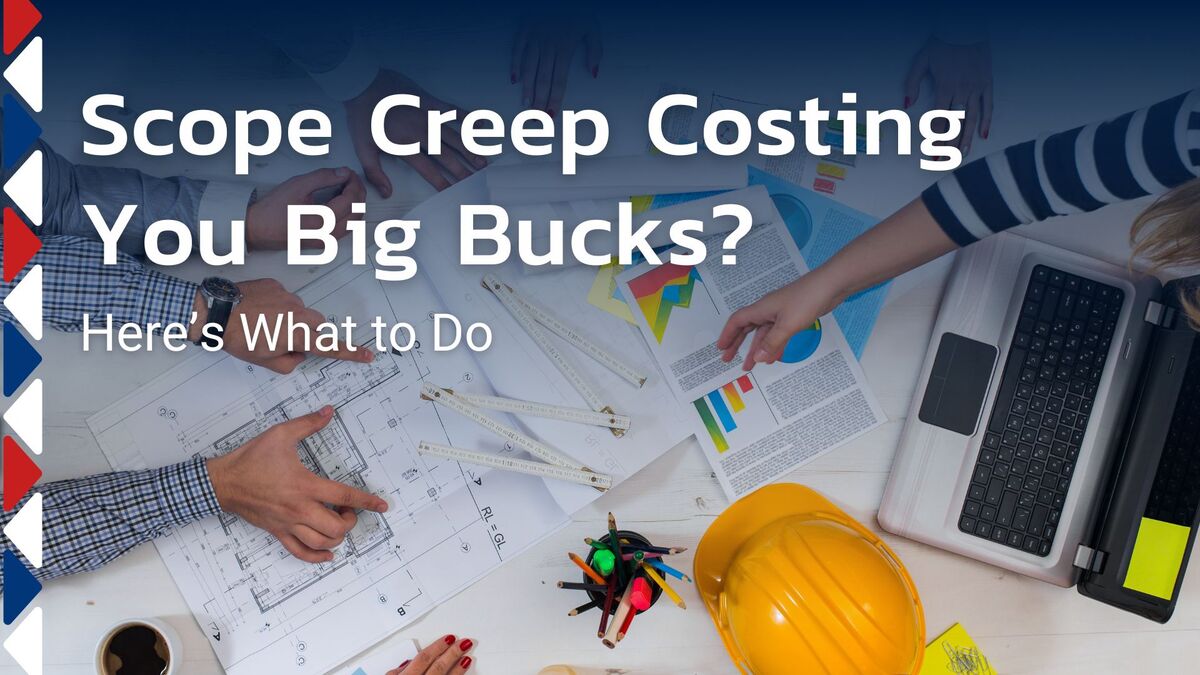
We've all seen it happen—you're managing a construction project, everything seems lined up perfectly, and suddenly, one tiny request leads to another. Before you know it, your budget has ballooned, your timeline is off track, and frustration levels are through the roof. Even something as minor as swapping out flooring or adding an unexpected design feature can quietly grow into a costly headache. If you're wondering exactly what effect scope creep has on a project, let's just say it's bigger than you'd expect—and expensive too.
In this guide, you'll learn exactly what scope creep in project management looks like, why it happens, how it affects project budgets, and—most importantly—what practical steps can help avoid it altogether. Proven strategies like Lean Construction and BIM technology are available to ensure projects stay within scope, budget, and timeline.
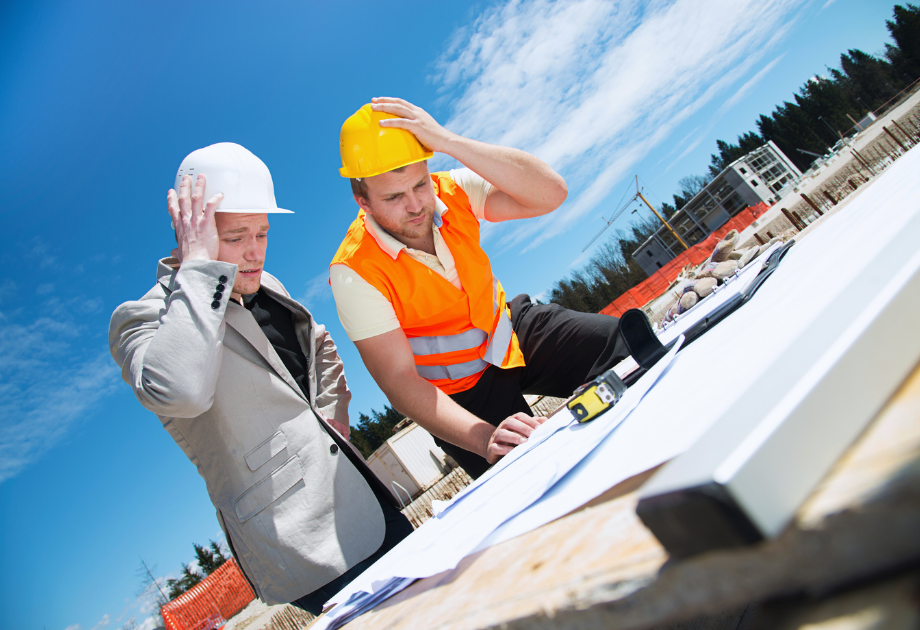
What Is Scope Creep, and Why Does It Matter?
Scope creep occurs when project requirements gradually expand beyond their original plan without proper oversight or management. It usually starts small—a client suggests a minor adjustment or a new idea emerges mid-construction—but these small suggestions rarely stay small.
Even minor alterations often create ripples throughout the entire project. Changing one detail might seem manageable at first, but it quickly impacts labor costs, material schedules, and administrative workloads. Knowing why scope creep happens is a foundational step toward keeping projects under control.
How Small Changes Lead to Big Expenses
Small design tweaks or unexpected substitutions often seem harmless, but each one impacts schedules and budgets more than teams might initially realize. Last-minute material substitutions can cause increased procurement costs, labor scheduling nightmares, and delays waiting for approvals. These seemingly minor adjustments can easily become big headaches for any project manager.
The Most Common Causes of Scope Creep
Scope creep doesn’t appear randomly. When things start going sideways, common issues include:
- Vague or incomplete project definitions
- Poor communication among stakeholders
- Last-minute client requests
- Regulatory changes
- Unforeseen site conditions
When stakeholders don't clearly understand what's expected from the start, it's easy to interpret details differently. Misunderstandings quickly turn into mistakes and costly rework. At Charles H. Hamilton, we've learned that precise planning and clear communication stop many scope creep problems before they start.
The True Cost of Scope Creep on Construction Projects
Scope creep isn't just inconvenient—it directly impacts your bottom line. To really grasp how damaging it can be, let's look at three cost areas: direct, indirect, and consequential expenses.
Direct Costs: Immediate Budget Hits
Direct costs include immediate expenses for labor, materials, and equipment. Bulk materials alone can account for up to 60% of a project’s total cost. Even a minor 10% overrun on these materials could increase the overall budget by roughly 6%. Over-ordering, even slightly, can raise costs by another 2–3%. Precise cost management is a powerful defense against these budget spikes.
Indirect Costs: Hidden Time Drains
Indirect costs emerge in the form of administrative overhead, project delays, and extra paperwork. Each time project requirements shift, managers and staff spend valuable hours managing these unexpected changes, sacrificing time better spent on productive project tasks.
Consequential Costs: The Ripple Effect
Finally, scope creep’s consequences stretch far beyond individual projects. Strained relationships with clients, contractors, or suppliers can quickly escalate into dissatisfaction, disputes, and even reputational harm. Poor scope management today risks losing opportunities tomorrow.
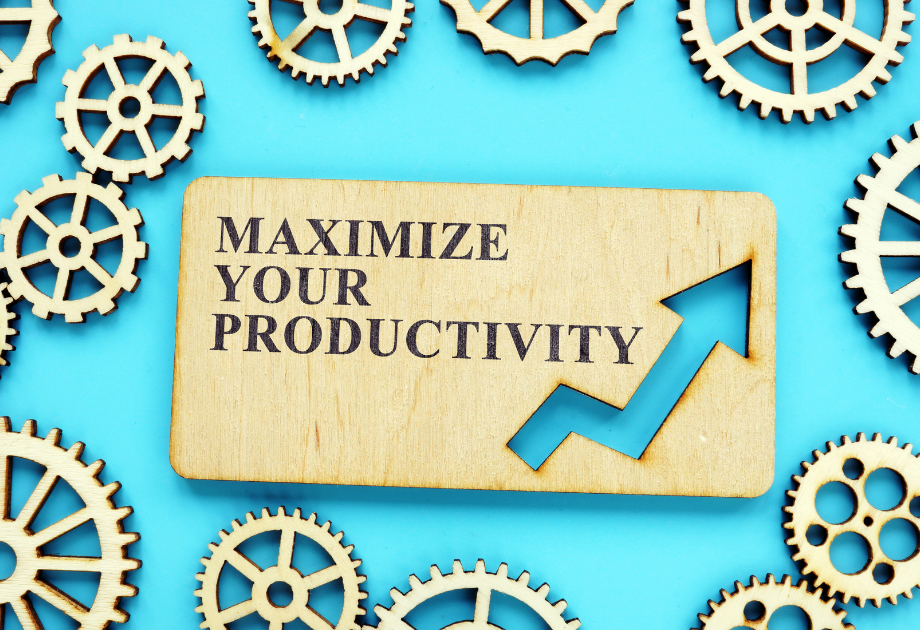
How Lean Construction Prevents Cost Overruns
Fortunately, there’s an effective way to combat scope creep. Lean Construction practices offer clear, proven methods to keep projects predictable and efficient. Charles Charles H.. Hamilton integrates these practices into every project to minimize waste, reduce costs, and maximize productivity.
Proactive Planning: Getting Ahead of the Curve
Lean Construction emphasizes thorough, detailed planning long before breaking ground. Collaborative pre-construction meetings involve all stakeholders, aligning expectations and resolving potential problems ahead of time. When everyone is aligned upfront, fewer unexpected scope adjustments arise mid-project.
Eliminating Waste with Just-in-Time Delivery
Lean principles also minimize unnecessary expenditures. Charles H. Hamilton uses just-in-time material deliveries to keep inventories low and prevent wasted resources. By ordering precisely what’s needed exactly when it’s needed, teams avoid costly surplus and unused bulk materials.
BIM: Using Tech to Tackle Scope Creep
Technology provides another powerful tool against scope creep: Building Information Modeling (BIM). BIM helps project teams visualize projects digitally before any physical work begins, catching and resolving problems long before they can drive up project costs.
Preventing Mid-Project Changes with Clear Visualization
BIM technology enables detailed digital modeling, helping teams spot potential design conflicts early. This significantly reduces the need for costly mid-project adjustments, ensuring budgets and timelines remain intact.
Accurate Budgeting You Can Trust
BIM offers precise, real-time data on materials, labor, and potential risks, greatly improving budget accuracy. By eliminating guesswork, projects remain transparent, predictable, and controlled throughout their lifecycle.
Practical Strategies for Managing Scope Creep
Implementing these practical strategies helps prevent scope creep from eroding your budget and timeline.
Define Your Scope Clearly
Clear scope definitions are the cornerstone of effective project management. Contracts should explicitly outline what’s included and excluded, creating firm boundaries. Having formal approval processes prevents unauthorized scope expansion.
Keep Everyone in the Loop
Structured communication channels—regular project updates, documented discussions, and clear approvals—help prevent misunderstandings. Good communication keeps everyone informed, aligned, and accountable.
Manage Change Orders Carefully
Change orders are inevitable, but they don’t need to escalate into budget disasters. Clear documentation, consistent review processes, and firm negotiation standards keep scope adjustments manageable. This disciplined approach keeps budgets and expectations transparent.
Keep Your Project on Track with Charles H. Hamilton’s Expertise
Scope creep may be common, but it’s certainly avoidable. Charles H. Hamilton specializes in using Lean Construction practices and advanced BIM technology to manage projects efficiently and proactively, ensuring scope remains firmly controlled. Teams provide accurate estimates, thorough planning, and proactive project oversight to keep clients within budget and on schedule.
If scope creep is draining your resources, contact Charles H. Hamilton’s experts today:
- Request Accurate Estimates →
- Explore Advanced Planning Techniques →
- Contact Charles H. Hamilton’s Team Today →
By partnering with Charles H. Hamilton, scope creep becomes manageable, construction projects become predictable, and budgets remain firmly under control—allowing teams to deliver quality results without unwanted surprises.